Произведен анализ разработок ИЭС им. Е.О.Патона в области автоматизированного ультразвукового контроля (АУЗК) труб, железнодорожных колес. Показан уровень этого оборудования и пути дальнейшего совершенствования. Сформулированы современные требования у установкам АУЗК и перспективы развития нового оборудования.
Автоматизированный ультразвуковой контроль (АУЗК) является наиболее распространенным способом неразрушающего контроля в промышленном производстве изделий различного назначения (трубы, железнодорожные колеса, прутки и т.п.). Повышение требований к качеству, увеличение скорости основных технологических операций при производстве изделий, необходимость повышения информативности и достоверности контроля обусловили повышение уровня автоматизации и визуализации УЗК. Эффективность АУЗК также во многом зависит также от согласованности с технологическим процессом изготовления изделий.
Современные установки АУЗК представляют собой сложные комплексы систем – механических, акустических, пневматических, гидравлических, электронных, связанных общим программным обеспечением.
Cовременные требования к установкам АУЗК
Конкуренция, существующая сегодня, например, в трубной промышленности, заставляет предприятия приобретать высококачественное оборудование для УЗ контроля отвечающее всем указанным выше требованиям.
С 2004 по 2007 год ОКТБ ИЭС им. Е.О.Патона разработало и поставило в Россию на ОАО «Выксунский металлургический завод» 9 установок АУЗК, обеспечивающих высокий уровень контроля:
Изображенная на рис. 1 схема УЗ контроля сварных швов труб с толщиной стенки до 50 мм обеспечивает контроль согласно требованиям API 5L, ISO 3183, DNV-OS-F101.
Несмотря на высокую скорость УЗ контроля (до 30 м/мин) используемая локально-иммерсионная акустическая головка обеспечивает высокую достоверность выявления дефектов и надежный акустический контакт. Инспекторы Европейского союза, контролирующие качество труб, выпускаемых на ОАО «ВМЗ», дали высокую оценку установкам АУЗК НК 360, 361, 362 именно по причине воспроизводимости результатов контроля при испытаниях в динамическом режиме на имитаторе дефектов, а также возможности просмотра и записи А-сканов обнаруженных дефектов.
Автоматизированный ультразвуковой контроль (АУЗК) является наиболее распространенным способом неразрушающего контроля в промышленном производстве изделий различного назначения (трубы, железнодорожные колеса, прутки и т.п.). Повышение требований к качеству, увеличение скорости основных технологических операций при производстве изделий, необходимость повышения информативности и достоверности контроля обусловили повышение уровня автоматизации и визуализации УЗК. Эффективность АУЗК также во многом зависит также от согласованности с технологическим процессом изготовления изделий.
Современные установки АУЗК представляют собой сложные комплексы систем – механических, акустических, пневматических, гидравлических, электронных, связанных общим программным обеспечением.
Cовременные требования к установкам АУЗК
- Соответствие методики АУЗК требованиям УЗ контроля, изложенным в нормативной технической документации на производство изделия.
- Достоверность выявления дефектов при высокой скорости проведения контроля.
- Высокая эксплуатационная надежность функционирования всех систем установки.
- Удобная компоновка акустических блоков с УЗ преобразователями, позволяющая до минимума сократить время калибровки акустической системы при перевалке оборудования на выпуск изделий другого типоразмера.
- Воспроизводимость результатов калибровки при повторных испытаниях в динамическом режиме на имитаторе дефектов.
- Развитая система визуализации процесса контроля и его результатов.
- Запись и хранение всех А-сканов от обнаруженных дефектов.
- Передача данных о результатах контроля каждого изделия в АСУ ТП цеха или завода.
Конкуренция, существующая сегодня, например, в трубной промышленности, заставляет предприятия приобретать высококачественное оборудование для УЗ контроля отвечающее всем указанным выше требованиям.
С 2004 по 2007 год ОКТБ ИЭС им. Е.О.Патона разработало и поставило в Россию на ОАО «Выксунский металлургический завод» 9 установок АУЗК, обеспечивающих высокий уровень контроля:
- 7 установок для АУЗК сварных швов и концевых участков труб диаметром 508 – 1420 мм (НК 360, НК 361, НК 362);
- 2 установки для АУЗК железнодорожных колес (НК 364).
Изображенная на рис. 1 схема УЗ контроля сварных швов труб с толщиной стенки до 50 мм обеспечивает контроль согласно требованиям API 5L, ISO 3183, DNV-OS-F101.
Несмотря на высокую скорость УЗ контроля (до 30 м/мин) используемая локально-иммерсионная акустическая головка обеспечивает высокую достоверность выявления дефектов и надежный акустический контакт. Инспекторы Европейского союза, контролирующие качество труб, выпускаемых на ОАО «ВМЗ», дали высокую оценку установкам АУЗК НК 360, 361, 362 именно по причине воспроизводимости результатов контроля при испытаниях в динамическом режиме на имитаторе дефектов, а также возможности просмотра и записи А-сканов обнаруженных дефектов.
Рис. 1. Схема расположения акустических головок при контроле продольных сварных соединений
- Д1, Д2 – лазерные датчики слежения за валиком усиления сварного шва;
- 1, 2, 3, 4 – группа наклонных ультразвуковых преобразователей для контроля на продольные дефекты;
- 5 – 16 – ультразвуковые преобразователи работающие в схеме типа «тандем»;
- 9 – 16 – ультразвуковые преобразователи, стоящие на сварном шве и работающие в иммерсионном варианте на обнаружение поперечных дефектов.
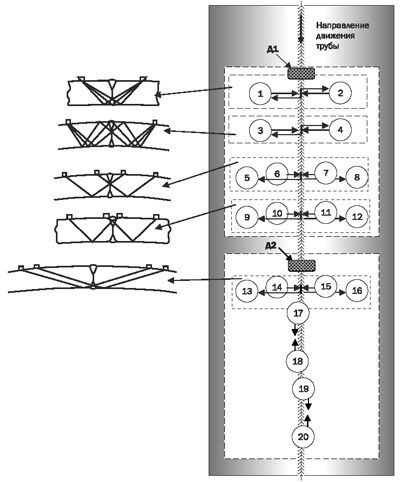
Рис. 3. Cхема расположения акустических головок при контроле концевых участков труб
- А – акустический блок для контроля на наличие продольных дефектов;
- Б – акустический блок для контроля на наличие расслоений.
- 1 – широкозахватные пленочные ПЭП, зона контроля 60 мм;
- 2 – иммерсионная ванна
- 3 – наклонные ПЭП с углами ввода 45º, зона контроля 30 мм;
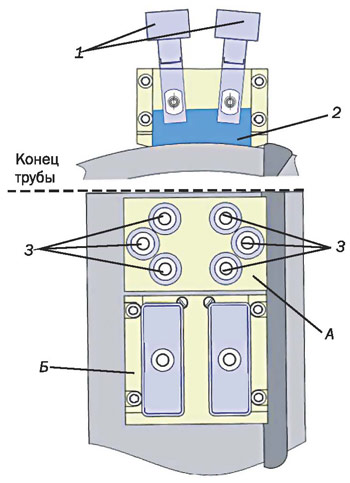
Общий вид установки для УЗК сварных швов представлен на рис. 2. Высокими акустическими характеристиками обладают и УЗ блоки для контроля концевых участков труб (рис. 3 и 4). Изображенная на рис. 3 схема расположения УЗ преобразователей в этих блоках обеспечивает за три оборота контроль зоны 100 мм на расслоение и 30 мм продольные дефекты.
Рис. 2. Установка НК 360 для АУЗК продольных сварных швов труб

- А – акустический блок для контроля на наличие продольных дефектов;
- Б – акустический блок для контроля на наличие расслоений.
- 1 – широкозахватные пленочные ПЭП, зона контроля 60 мм;
- 2 – иммерсионная ванна
- 3 – наклонные ПЭП с углами ввода 45º, зона контроля 30 мм;
Рис. 4. Акустические блоки для контроля концевых участков труб: акустические блоки для контроля на наличие расслоений (1) и на наличие продольных дефектов (4)
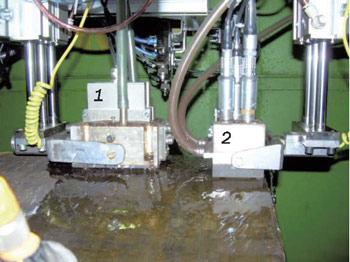
При выборе основных схем контроля сварных швов и концевых участков труб, помимо стандартов API 5L, ISO 9765, учитывались дополнительные технические требования завода по ширине контролируемых концевых участков труб. Наиболее удачная конструкция локально-иммерсионных акустических блоков с иммерсионными УЗ преобразователями установки НК 362М показана на рис. 4.
На рис. 5 изображена схема расположения акустических пьезопреобразователей при контроле железнодорожных колес(установка НК 364). Выбор схемы УЗ контроля железнодорожных колес определялся на основе руководящих материалов МПС России РД 32.144-2000 с дополнениями. Этот документ предусматривает обнаружение наиболее часто встречающихся дефектов, а также дефектов, сильно влияющих на безопасность эксплуатации.
На рис. 5 изображена схема расположения акустических пьезопреобразователей при контроле железнодорожных колес(установка НК 364). Выбор схемы УЗ контроля железнодорожных колес определялся на основе руководящих материалов МПС России РД 32.144-2000 с дополнениями. Этот документ предусматривает обнаружение наиболее часто встречающихся дефектов, а также дефектов, сильно влияющих на безопасность эксплуатации.
Рис. 5. Схема расположения УЗ преобразователей и зоны контроля установки НК 364:
а – контроль обода в осевом направлении и контроль наклонными ПЭП; б – контроль диска; в – контроль ступицы; г – контроль обода в радиальном направлении; д – Расположение ПЭП при контроле реборды; е – Расположение ПЭП при контроле наклонными датчиками; 1-6 – наклонные ПЭП для контроля обода, 7-9 – прямые ПЭП контроля обода в осевом направлении; 10 – наклонный ПЭП для контроля реборды; 11-14 – прямые ПЭП для контроля диска; 15-17 – прямые ПЭП контроля обода в радиальном направлении; 18 – прямой ПЭП для контроля ступицы.
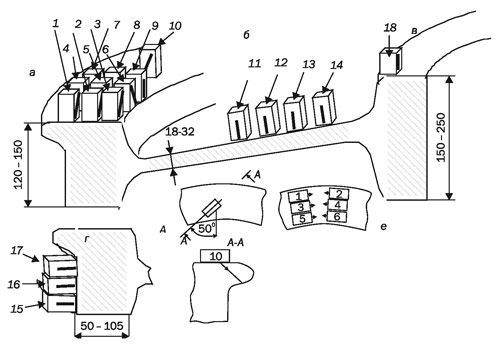
В обоих случаях контроль ведется эхо-импульсным методом продольными и поперечными волнами на частотах 2,5 и 5,0 МГц. Учитывая высокие скорости контроля (до 30-40 м/мин) также был выбран локально-иммерсионный способ создания акустического контакта. Были разработаны локально-иммерсионные акустические блоки с иммерсионными УЗ преобразователями на основе композитной пьезокерамики фирмы Panametrics (Рис. 6).
Рис. 6. Акустические блоки для контроля ступицы (а) и поверхности катания (б)
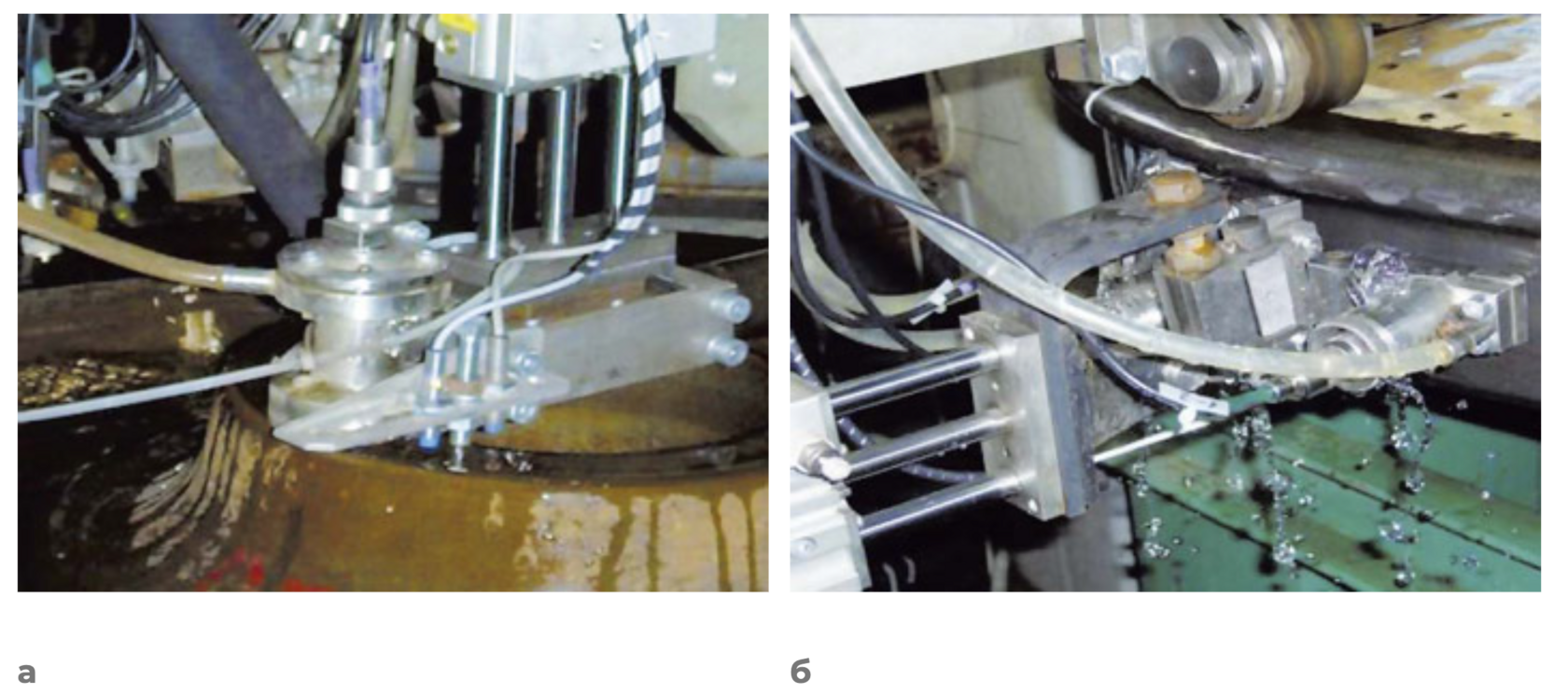
Это позволило надежно осуществлять контроль акустического контакта по всем УЗ каналам и иметь соотношение сигнал/шум не хуже 16 Дб. Кроме того, локально-иммерсионный способ получения акустического контакта не так критичен к качеству поверхности контролируемых изделий. Учитывая перспективу изготовления в будущем колес с S-образным диском был разработан специализированный сменный блок для УЗ контроля таких колес (Рис. 7 а,б).
Рис. 7. Модуль для контроля S-образного диска. Общий вид блока (а) и акустическая головка (б).
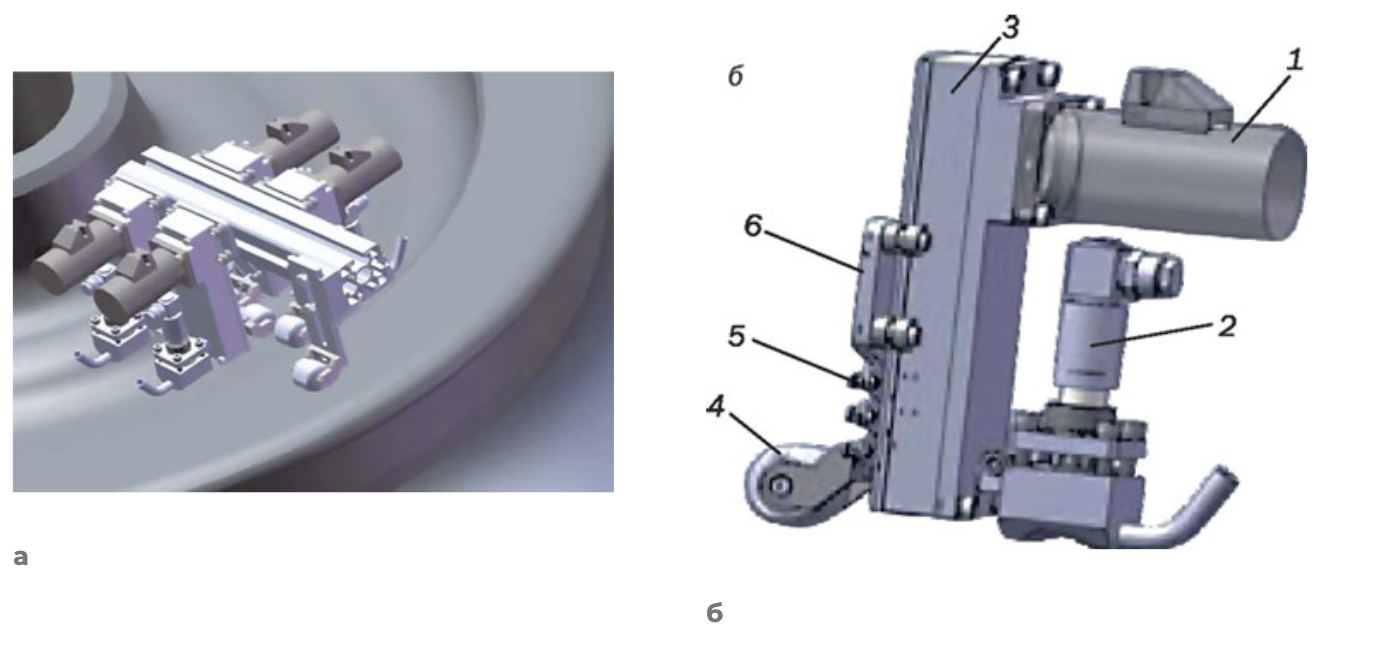
Основной особенностью этого блока является отсутствие контакта акустических блоков с контролируемой поверхностью. В данной конструкции акустического блока нет башмака, единственным соприкасающимся с колесом звеном является ролик, который поворачивается с помощью электроприводов вместе с корпусом датчика во время перехода на последующую дорожку.
При калибровке на имитаторе дефектов выбираются необходимые углы наклона УЗ преобразователей для установки их перпендикулярно касательной поверхности контроля. В дальнейшем программа автоматически выставит заданные углы при сканировании диска.
В процессе контроля на каждом шаге УЗ датчики поворачиваются электродвигателями на определенный в процессе калибровки угол.
Универсальный ультразвуковой дефектоскоп НК 363 выполнен на базе ультразвуковых плат французской фирмы «Socomate». Они представляют собой PCI платы полного размера для установки в шасси промышленного компьютера, предназначены для создания ультразвуковых дефектоскопов различной сложности и для реализации различных схем контроля. Это очень удобно для реализации различных задач контроля.
Непосредственно плата производит усиление, фильтрацию и оцифровку сигнала, цифровую обработку и предварительное хранение в памяти самой платы для дальнейшей передачи пакетами в ОЗУ компьютера с использованием режима DMA. Предусмотрен высокоскоростной сбор данных в режиме А-, С-скана. Продукция хорошо известна (в Европе, Северной Америке, Азии, Африке) и широко используется такими известными фирмами, как «Rolls-Royce», «Pratt&Whitney» и «GE».
Система управления установками выполнена на базе универсального программируемого контроллера Simatic S7-300 (Siemens), станций распределенного ввода/вывода ЕТ-200, и паненей оператора ОР-170 В. Обмен между участниками сети производится по шине PROFIBUS-DP. Система управления позволяет оператору осуществлять диагностику работы датчиков и приводов по выводимой информации на экран дисплея пульта управления. В случае отказов оборудования на экран выводится информация о возможной причине неисправности и позволяет быстро ее обнаружить и устранить.
Программирование контроллера системы управления выполнено стандартными инжиниринговыми средствами на базе программного пакета STEP 7. Разработанное программное обеспечение сбора и обработки данных УЗ контроля носит универсальный характер и может выполнять требования любых задач УЗ контроля.
Система визуализации процесса и результатов контроля на установках обеспечивает выдачу максимальной информации оператору в режиме реального времени. Интерфейс программного обеспечения обеспечивает простоту и удобство работы, как в режиме калибровки системы, так и в процессе проведения контроля.
На каждый проконтролированный объект выдается полный протокол контроля с выводом основных параметров контроля и информации об обнаруженных дефектах (рис. 8а). Реализована архивация результатов контроля с возможностью просмотра файлов данных по каждому проконтролированному объекту. В файлах данных сохраняется вся информация об обнаруженных дефектах, реализован просмотр А-сканов по выбранному дефекту (рис. 8б,в). Протоколы контроля каждого проконтролированного изделия передаются в систему АСУ ТП цеха.
При калибровке на имитаторе дефектов выбираются необходимые углы наклона УЗ преобразователей для установки их перпендикулярно касательной поверхности контроля. В дальнейшем программа автоматически выставит заданные углы при сканировании диска.
В процессе контроля на каждом шаге УЗ датчики поворачиваются электродвигателями на определенный в процессе калибровки угол.
Универсальный ультразвуковой дефектоскоп НК 363 выполнен на базе ультразвуковых плат французской фирмы «Socomate». Они представляют собой PCI платы полного размера для установки в шасси промышленного компьютера, предназначены для создания ультразвуковых дефектоскопов различной сложности и для реализации различных схем контроля. Это очень удобно для реализации различных задач контроля.
Непосредственно плата производит усиление, фильтрацию и оцифровку сигнала, цифровую обработку и предварительное хранение в памяти самой платы для дальнейшей передачи пакетами в ОЗУ компьютера с использованием режима DMA. Предусмотрен высокоскоростной сбор данных в режиме А-, С-скана. Продукция хорошо известна (в Европе, Северной Америке, Азии, Африке) и широко используется такими известными фирмами, как «Rolls-Royce», «Pratt&Whitney» и «GE».
Система управления установками выполнена на базе универсального программируемого контроллера Simatic S7-300 (Siemens), станций распределенного ввода/вывода ЕТ-200, и паненей оператора ОР-170 В. Обмен между участниками сети производится по шине PROFIBUS-DP. Система управления позволяет оператору осуществлять диагностику работы датчиков и приводов по выводимой информации на экран дисплея пульта управления. В случае отказов оборудования на экран выводится информация о возможной причине неисправности и позволяет быстро ее обнаружить и устранить.
Программирование контроллера системы управления выполнено стандартными инжиниринговыми средствами на базе программного пакета STEP 7. Разработанное программное обеспечение сбора и обработки данных УЗ контроля носит универсальный характер и может выполнять требования любых задач УЗ контроля.
Система визуализации процесса и результатов контроля на установках обеспечивает выдачу максимальной информации оператору в режиме реального времени. Интерфейс программного обеспечения обеспечивает простоту и удобство работы, как в режиме калибровки системы, так и в процессе проведения контроля.
На каждый проконтролированный объект выдается полный протокол контроля с выводом основных параметров контроля и информации об обнаруженных дефектах (рис. 8а). Реализована архивация результатов контроля с возможностью просмотра файлов данных по каждому проконтролированному объекту. В файлах данных сохраняется вся информация об обнаруженных дефектах, реализован просмотр А-сканов по выбранному дефекту (рис. 8б,в). Протоколы контроля каждого проконтролированного изделия передаются в систему АСУ ТП цеха.
Рисунок 8.
Просмотр результатов на установке НК 364:
а – протокол контроля колеса; б – дефектограмма. На дефектограмме концентрическими окружностями зоны контроля. Каждая из зон разбита на участки, соответствующие каждому из каналов. При обнаружении дефекта на дефектограмме отображается пятно красного цвета в соответствующей зоне. в – программа просмотра результатов контроля в режиме просмотра А-скана.
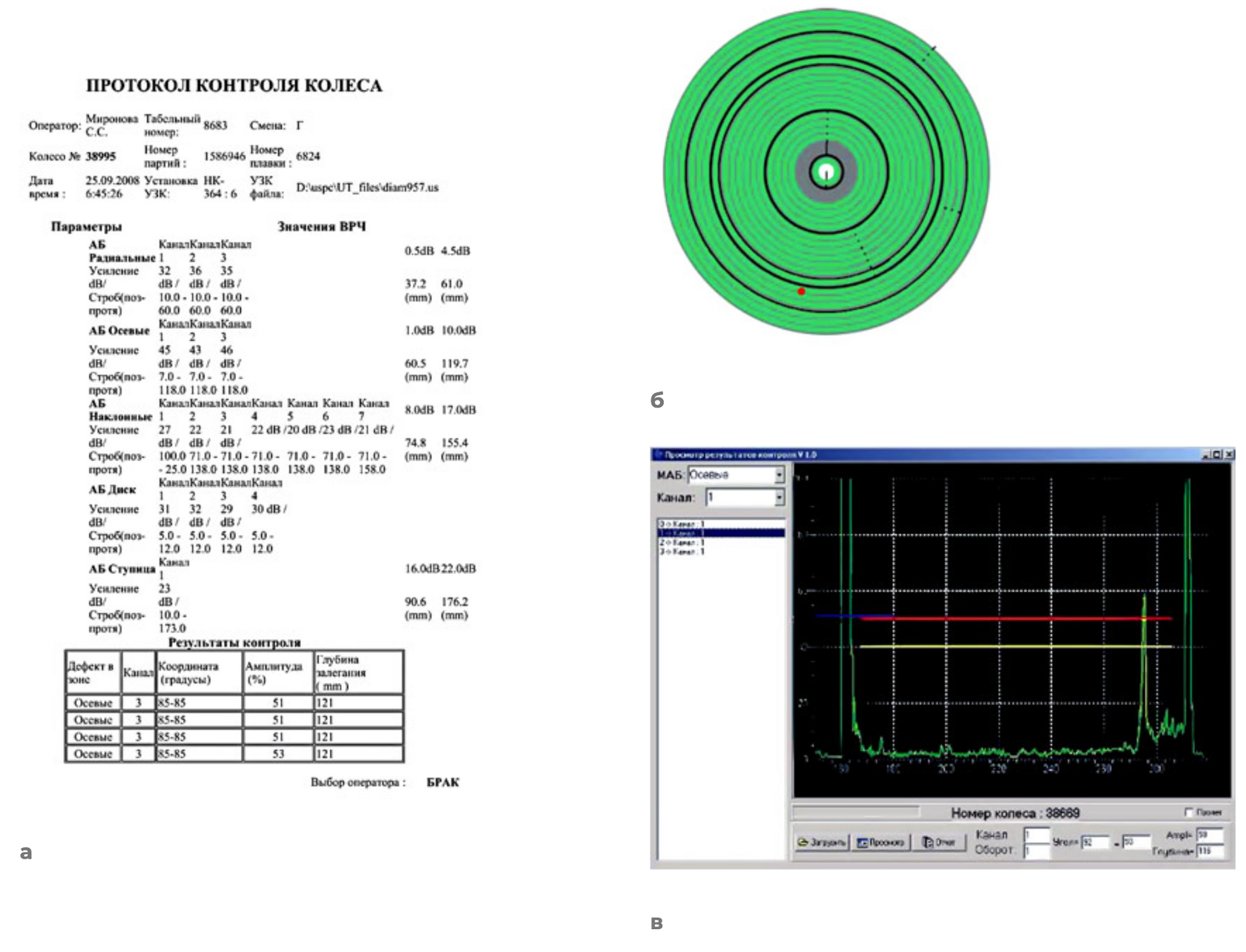
Необходимость в удовлетворении растущих требований к скорости контроля, повышение уровня чувствительности, надежности систем АУЗК требует применения новых технологических решений, таких как:
Одним из вариантов этой технологии является технология FAAST II, которая позволяет произвести замену нескольких одиночных УЗ преобразователей с разными углами ввода на один преобразователь на базе 2D-матричных фазированных решеток, который может формировать одновременно несколько УЗ лучей с разными углами ввода в разных плоскостях.
Сейчас в ИЭС им. Е. О. Патона разрабатывается оборудование для АУЗК тела труб с применением этой технологии. Основные преимущества технологии FAAST II по сравнению с классической технологией ФАР:
- Применение иммерсионных преобразователей на основе композитной керамики, которые излучают более короткие импульсы и обладают большей абсолютной чувствительностью. Их применение обеспечивает уменьшение «мертвой» зоны.
- Использование систем «преобразователь + дефектоскоп» с фазированными решетками, позволяющих управлять полем преобразователя для изменения угла ввода в широких пределах с помощью электронных устройств.
Одним из вариантов этой технологии является технология FAAST II, которая позволяет произвести замену нескольких одиночных УЗ преобразователей с разными углами ввода на один преобразователь на базе 2D-матричных фазированных решеток, который может формировать одновременно несколько УЗ лучей с разными углами ввода в разных плоскостях.
Сейчас в ИЭС им. Е. О. Патона разрабатывается оборудование для АУЗК тела труб с применением этой технологии. Основные преимущества технологии FAAST II по сравнению с классической технологией ФАР:
Значительное увеличение производительности контроля;
Возможность обнаружения «косых» дефектов, что необходимо при контроле бесшовных труб
Более низкая стоимость преобразователей и электронного оборудования по сравнению с классической технологией ФАР.
Характерной особенностью программной обработки FAAST II является возможность одновременного просмотра А-сканов каждого луча по аналогии с традиционными системами. Это привычно для операторов.
Пример дефектограммы с дефектами на стандартном образце, в том числе и косыми, показан на рис.
Пример дефектограммы с дефектами на стандартном образце, в том числе и косыми, показан на рис.
Рис. 9. Дефектограмма FAAST II
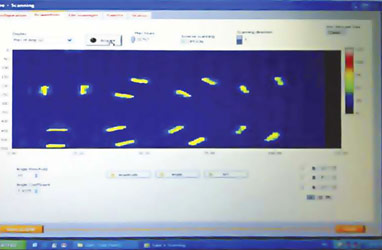
- Использование при контроле криволинейных поверхностей (например, S-образного диска ж/д колес) автоматического слежения акустического блока за профилем поверхности.
- Совершенствование программного обеспечения дефектоскопа для повышения уровня помехозащиты и наглядности визуализации результатов контроля.
- И, наконец, совмещение в одном автоматизированном оборудовании двух методов. Например, помимо традиционного УЗК, можно применить для обнаружения поверхностных дефектов вихретоковый метод контроля.
Выводы
Возрастающие требования к качеству сварных труб, железнодорожных колес и т.п. требует постоянно повышать уровень неразрушающего контроля. На примерах разработок ИЭС им. Е.О.Патона показаны достижения в этой области. Разработанные средства АУЗК обеспечивают высокую достоверность обнаружения дефектов и высокую эксплуатационную надежность.
Литература
- Неразрушающий контроль: Справочник: В 7т. / под редакцией академика РАН В.В.Клюева М. Машиностроение, 2004г. Т 3. 860с.
- Найда В.Л., Мозжухин А.А., Лобанов О.Ф. Новое поколение оборудования для УЗК сварных труб. Журнал “Автоматическая сварка” сентябрь 2004г. С.58-62.
- Ткаченко А.А., Найда В.Л., Копылов А.П. Обеспечение надежности автоматизированного УЗК сварных труб при их производстве. Журнал “В мире неразрушающего контроля” 3.2006г. С.17-20.
- Найда В.Л.Система управления АУЗК железнодорожных колес на Выксунском металлургическом заводе. Журнал “Техническая диагностика и неразрушающий контроль” 2.2008г. С.50-52.